절삭 이론
1. 절삭 가공의 종류
종류 | 설명 | |
절삭날에 의한 가공 | 단인공구에 의한 가공 | - 선삭 (선반 가공) - 평삭 (셰이퍼, 슬로터, 플레이너) |
다인공구에 의한 가공 | 밀링, 드릴링, 보링 | |
입자의 의한 가공 | 연삭 숫돌(Grinding ston)에 의한 가공 | 연삭, 호닝 (honing), 슈퍼 피니싱 |
분말 입자()에 의한 가공 | 액체 호닝 (liquid honing), 래핑, 초음파 가공 |
2. 칩의 종류와 형태
칩의 종류 | 가공물의 재질 | 경사각 | 절삭 속도 | 절삭 깊이 | 설명 |
유동형 칩 (Continous chip, Flow type chip) |
연하고 점성이 큼 | 큼 | 빠름 | 작음 | • 연성재료 (Soft material: 구리, 알루미늄 등)을 a) 고속 절삭 시 b) 윗면 경사각(Top rake angle)이 클 때 c) 절삭 깊이(Depth of cut)가 작을 때 d) 유동성 있는 절삭유를 사용할 때 e) 커팅 도구가 날카로운 Edge를 가지는 경우 • 연속적인 칩이며 가장 이상적인 칩 • 연속적으로 칩이 생기기 때문에 진동이 적어 표면이 깨끗 |
전단형 칩 (Discoutinous chip, Shear type chip) |
↓ | ↓ | ↓ | ↓ | • 연성재료 (Soft material: 구리, 알루미늄 등)을 a) 저속 절삭 시 (Low feed rate) b) 윗면 경사각이 작을 때 e) 절삭 깊이가 클 때 • 칩이 경사면 위를 원할하게 흐르지 못해서, 절삭 공구가 칩을 밀어내는 압축력이 커지면서 발생 • 칩의 두께가 수시로 변해 진동이 발생하기 쉬움 • 표면 품질이 좋지 않음 |
열단형(경작형) 칩 (Tear type chip) |
↓ | ↓ | ↓ | ↓ | • 점성 재료 절삭 시 a) 경사각이 작은 절삭 공구로 작업할 때 & 절삭 깊이가 클 때 |
균열형 칩 (Crack-type chip) |
굳고 취성이 큼 | 작음 | 느림 | 큼 | • 주철과 같은 취성재료(Brittle material)을 저속 절삭 시, 진동 때문에 날 끝에 작은 파손이 생김 - 채터(Chatter) 발생 확률이 큼 |
3. 구성인선 (Built up edge)
설명: 연성재료를 절삭 시, 칩이 고온, 고압으로 공구 인선에 응착하여, 실제의 절삭날 역활을 하는 것
생성 주기: 발생 -> 성장 -> 분열 -> 탈락
영향
- 공구에 진동을 일으킴
- 기공면이 거침
- 공구 수명이 단축
- 마멸(Attriction)이 심함
- 가공수치가 작아짐
- 동력손실이 큼
방지법
- 윗면 경사각, 절삭 속도를 크게 함
- 유동성있는 절삭유 사용
- 절삭 공구의 인선(Edge)를 예리하게 함
- 마찰 계수가 작은 절삭 공구를 이용
절삭 저항
1) 절삭 저항의 3분력: 주분력 (Principal cutting force) > 배분력 (Radial force, Back force) > 횡분력(또는 이송분력, Feed force)
2) 절삭 저항력에 영향을 미치는 요소
• 경질 재료 (Hard material)일수록 증가
• 고속일수록 감소
• 공구의 날끝각, 경사각이 클수록 감소
• 절삭 면적이 클수록 증가
절삭 역학
1) 가공면의 표면 거칠기 (조도, Surface roughness)
- 조도에 영향을 주는 인자: 절삭 속도, 절삭제, 바이트 형상, 크기, 이송 (Feed), 절삭 깊이 (Depth of cut), 공작물 재질 등,...
절삭속도 (절삭깊이) | 증가 (감소) | • 구강인선 소멸 • 절삭 저항이 감소되어 표면 거칠기 양호 |
감소 (증가) | • 구강인선 생성 • 절삭 저항 증가로 인한 표면 거칠기 증가 |
절삭 동력 (Cutting power)
• F: 주분력
• V: 절삭속도 (m/min)
절삭 온도
절삭열의 형태:
(1) 전단면에서 전단 소성변형 (Plastic deformation)에 의한 열
(2) 칩과 절삭 공구 경사면의 마찰열
(3) 공작물에서 칩이 분리될 때 생기는 마찰열
절삭온도와 절삭 조건의 관계
요소 | 절삭온도 | 결과 |
• 절삭속도 증가 | • 절삭 속도와 비례하여 증가 • 공구나 공작물로 전달되는 열에 비해 칩으로 방출되는 열의 비중이 커짐 |
• 공구 연화 (Tool softening) • 공구 마멸 (Attriction) 촉진 • 공구 수명 감소 |
• 공작물 경도, 강도 증가 • 열전도도 작음 |
• 절삭온도 증가 |
고온절삭 및 저온 절삭
1. 고온 절삭 200-800도로 가열하여 절삭, 재로의 경도가 떨어져 절삭 저항 감소
2. 저온 절삭: -20~-150도로 냉각하여 절삭, 공구의 마멸이 작아지고 절삭 능력 향상
절삭열의 온도의 측정 방법:
(1) 칩의 색깔에 의한 측정
(2) 열량계에 의한 측정
(3) 열전대에 의한 측정
(4) 복사 고온계에 의한 측정
(5) 공구와 공작물간 열전대 접촉에 의한 측정
(6) 시온도료에 의한 측정
(7) PBS 광전지를 이용한 측정
절삭유
1. 절삭유의 사용 목적: 냉각 작용, 윤활 작용, 세척 작용
1) 냉각 작용 및 윤활 작용: 절삭공구와 칩 사이의 마찰 저항 감소 및 절삭열 감소로 인한 정밀도 저하 방지
2) 공구의 인선을 냉각시켜 연화(Softening) 방지 및 공작물의 정밀도 저하 방지로 인한 공구 수명 연장과 절삭성능의 향상
3) 세척 작용: 칩 제거 및 공작물 표면의 산화 방지
2. 절삭유의 조건
1) 냉각성, 윤활성 (Lubricity), 유동성 (Liquidity) 우수
2) 휘발성 (Volatility)이 없고, 인화점 및 발화점 (flash point)가 높아야 함
3) 칩분리가 용이하고 회수가 쉬어야 함
4) 마찰계수가 작아야 함
5) 화학적으로 안전하며 인체에 무해해야 함
3. 절삭유의 종류
종류 | 설명 |
수용성 절삭유 (Soluble Oil) |
• 광물성유를 화학적으로 처리하여 원액과 물을 혼합하여 사용 • 표면활성제(Surfactant)와 부식방지제(Corrosion inhibitor)를 첨가하여 사용 • 점성이 낮고 비열이 커서 냉각효과가 큼 • 고속 절삭 및 연삭 가공액으로 주로 사용 |
유화유 (Emulsion oil) |
• 광유에 비눗물을 첨가하여 유화한 것 • 냉각작용이 비교적 크며, 윤환성이 있고 값이 저렴하여 광범히하게 사용 |
광유 (Mineral oil) |
• 경유, 머신 오일, 스핀들 오일, 석유 및 기타의 광유 • 윤활성은 좋으나 냉각성이 적어 경절삭에 주로 사 |
4. 절삭유의 급유 방법
절삭 공구 (Cutting tool)
1. 절삭 공구의 구비 조건
(1) 고온경도 (Hot hardness), 내마멸성(Abrasion resistance), 강인성(Toughness)이 커야 함
(2) 마찰계수가 작아야 함
(3) 가격이 저렴하고 구입이 용이해야 함
2. 절삭 공구의 종류
종류 | 설명 |
탄소공구강 (STC) (Carbon Tool Steel) |
|
합금공구강 (STS) (Alloy Tool Steel) |
|
고속도강 (SKH) |
|
초경합금 | |
주조경질합금 | |
세라믹 | • 고온 경도가 가장 높다 • 충격 및 진동에 약함 • 냉각제를 쓰지 않음 |
서멧 | |
다이아몬드 | • 경도가 가장 높다 |
CBN 공구 | • 세라믹, 초경합금보다 경도가 높다 |
Milliing Machine
- used to produce plane surfaces and grooves or channels in plane surfaces
Several tools used in milling machines
cutters | Descriptions |
평면 커터 Plain milling cutter) |
▪ 평면 절삭, 소비동력이 적음 ▪ 가공면의 정도가 좋음 ▪ have teeth only on the periphery ▪ used for milling flat surfaces |
측면 커터 (Side milling cutter) |
▪ have cutting edges on the periphery ▪ used to mill a channel or groove |
엔드밀 (end mill) |
▪ |
정면 커터 (Face cutter) |
▪ 넓은 평면을 가공할 때 사용 |
총형 커터 (Formed cutter) |
▪ 기어 또는 리머 가공 |
볼엔드밀 밀링 커터 (Ball end milling cutter) |
▪ 복잡한 형상의 가공 |
각 커터 (Angle Cutter) |
▪ 각도 절삭 |
Fly cutter |
▪ consist of a cylinder with a single movable cutting edge ▪ used for cutting round holes and milling large surfaces |
Radial Saw | ▪ used for cutting narrow grooves |
Two possible cutting operations
밀링 작업
1. 두 가지 작동 방법
절삭 종류 | 설명 |
상형절삭 (Conventional milling, upmilling) |
▪ 정의: Cutting Edge의 회전 방향이 Feed 방향이 반대 - Cutter가 작업물의 표면과 만나는 지점에서 Cutting 방향과 Feed의 방향이 반대 ▪ 장점 a) 기계에 무리를 주지 않음 b) 날이 부러질 염려가 없음 c) 칩이 날을 방해하지 않음 d) 절삭열에 의한 치수 정밀도의 변화가 적음 e) 백래기 발생이 없음 ▪ 단점 a) 작업물의 고정이 불안정하며 떨림이 일어나기 쉬우며 동력 손실이 많음 b) 커터의 마멸 (attrition)이 심하며 수명이 짧음 c) 가공면이 거침 |
하향 절삭 (Climb milling or Down milling ) |
▪ 정의: 밀링커터의 회전 방향과 공작물의 이송방향 (Feed)이 동일 - 즉, 밀링 커터가 작업물의 위에서 아래로 깎음 ▪ 장점 a) 커터의 마멸이 적고 수명이 길음 b) 공작물의 고정이 안정하며 동력 손실이 적음 c) 날 하나마다의 간격이 짧아 가공면이 깨끗 (clear cut) d) 가공할 면을 잘 볼 수 있음 (즉, 시야가 좋음) ▪ 단점 a) 기계에 무리를 주며 날이 부러지기 쉬움 b) 칩이 커터와 공작물 사이에 끼어 절삭을 방해 c) 절삭열에 의한 치수 정밀도 변화가 큼 d) 백래시가 발생 |
상향절삭 | 하향절삭 | |
백래시 | 절삭에 별 지장이 없음 | 백래시를 제거해야 함 |
기계의 강성 | 강성이 낮아도 무관 | 가공할 때, 충격이 있어 높은 강성이 필요 |
가공물의 고정 | 절삭력이 상향으로 작용하므로 고정이 불리 | 절삭력이 하향으로 작용하므로 고정에 유리 |
인선의 수명 | 마찰열로 마모가 빠르고 공구 수명이 짧음 | 상향절삭에 비해 수명이 김 |
마찰저항 | 마찰저항이 큼 | 마찰력은 적으나 하향으로 충격력이 작용 |
표면 거칠기 | 전체적으로 하향절삭보다 나쁨 |
1. End mill
선반 (Lathe )
척의 종류
1. Relavent Equations in Lathe
1) Cutting Speed (절삭속도)
where V is the cutting speed, d is the diameter of the cut object (mm), and N is the rpm of the principle axis.
• economical cutting speed
2) Cutting time (절삭 시간)
\begin{equation}
T = \frac{l}{N S} \text{(min)}
\end{ equation }
where l is the length of the object and S is the feed speed in (mm/rev)
• feed speed (이송속도): the distance of bite when the object is rotated once.
3) Cutting power
바이트 (Bite)
바이트의 기본 각도 | 설명 |
윗면 경사각 (Top Rake Angle) |
• 칩의 흐름을 좋게 하는 각 • 클수록 절삭력이 좋고 공작물의 표면이 깨끗 • 공작물의 경도가 높을 수록 작게하며 음의 값을 갖도록 함 |
앞면 여유각 (Front clearance angle, relief angle) |
• 공작물과의 마찰을 피하기 위한 각 • 클수록 날이 약하게 됨 |
압면 공구각 (Wedge angle) |
인서트 팁 규격
규격 | 클램프방식 | 인서트 형상 | 팁의 여유각 | 공차 (Tolerance) |
단면형상 | 절삭길이 | 두께 | 반지름 |
설명 | • S: 정사각형 • R: 원형 • T: 삼각형 |
• N: 0' • P: 11' • E: 20' |
• A: 정밀급 • M: 보통급 |
1.
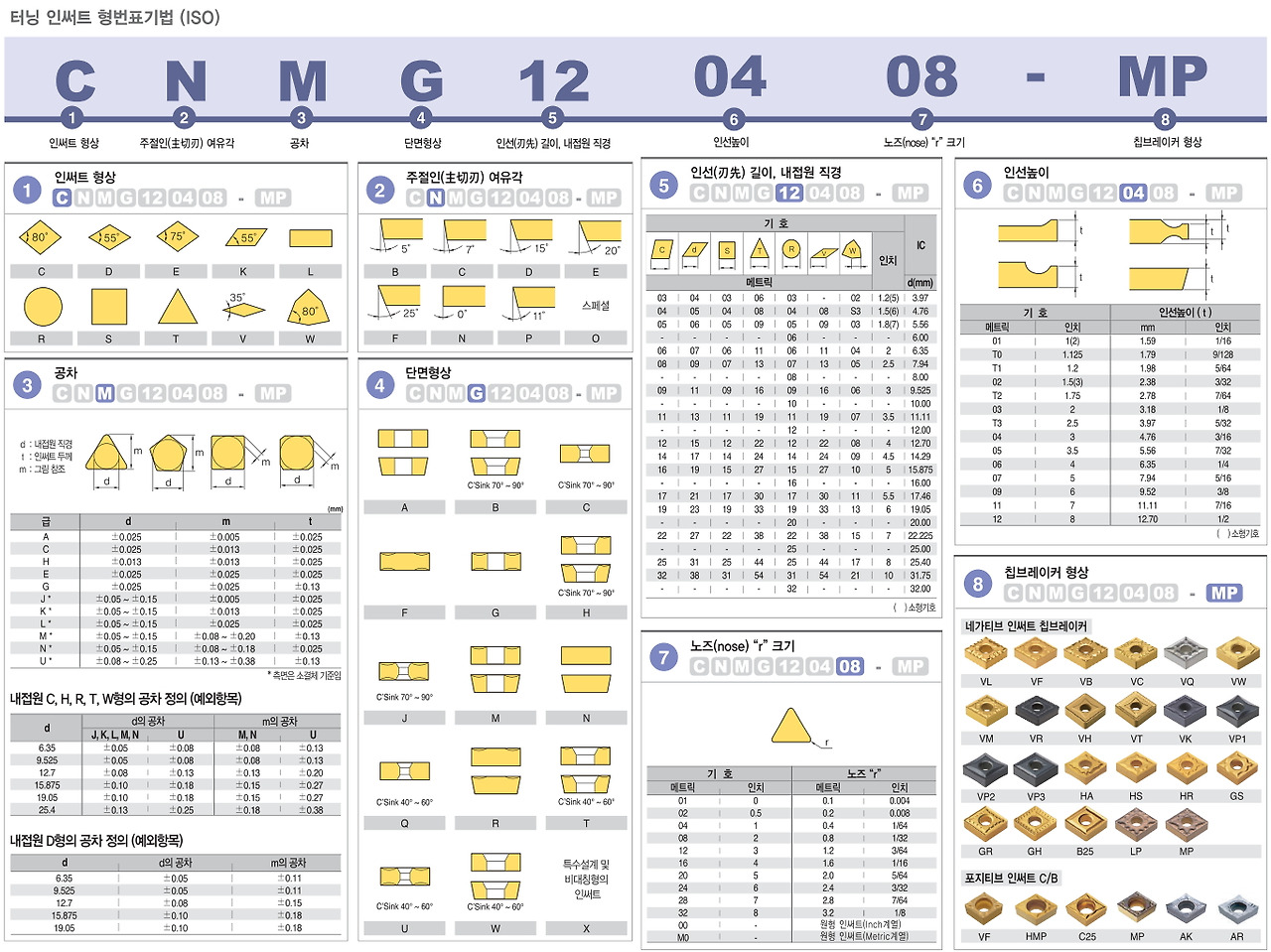
드릴링머신
드릴링의 기본 작업: 드릴링, 리밍 (Reaming), 태핑 (Tapping), 보링, 스풋 페이싱, 카운터 보링, 카운터 싱킹
드릴링 (Drilling) |
드릴로 구멍을 둟는 작업 |
리밍 (Reaming) |
▪ 드릴로 이미 뚫은 구멍을 정밀하게 다듬는 작업 |
태핑 (Tapping) |
▪ 탭을 이용하여 암나사를 가공하는 작업 |
보링 (Boring) |
▪ 이미 뚫은 구멍의 내경을 넓히는 작업 |
스폿 페이싱 | ▪ 볼트나 너트등을 고정할 때, 접촉부가 안정되게 하기 위하여 자리를 만드는 작업 |
카운터 보링 | ▪ 작은 나사, 둥근 머리 볼트의 머리 부분이 공작물에 묻힐 수 있도록 단이 있는 구멍을 뚫는 작업 |
카운터 싱킹 | 접시머리나사의 머리부를 묻히게 하기 위해 원뿔 자리를 만드는 작업 |
드릴 (Drill)
1. 드릴의 종류
종류 | 설명 |
트위스트 드릴 | ▪ 가장 널리 사용 ▪ 절삭력이 좋고 칩의 배출이 좋음 |
평드릴 | ▪ 날 끝의 안내가 없어 구멍이 휘어지기 쉬움 |
직선홈드릴 | ▪ 황동이나 얇은 판의 구멍을 뚫기에 사용 ▪ 절삭성이 떨어짐 |
유공드릴 | ▪ 깊은 구멍 가공시 사용 ▪ 칩의 배출 용이 |
센터 드릴 | ▪ 센터 구멍을 뚫을 때 사용 |
'공학(Engineering) > 기계 공학' 카테고리의 다른 글
[기계공학] Tap/Screw에 대해서 (0) | 2024.01.11 |
---|
댓글